In order to really evaluate the costs of the company, directed to the production of products or the provision of services, a special methodology is applied. Functional-cost analysis is a special technology with which you can estimate the value without reference to the organizational structure of the company. This tool allows managers to better understand production relationships and processes. Features of this method, its main features and recommendations for use will be discussed later.
Purpose and features of the technique
Functional cost analysis (PSA) is a method that allows you to determine not only the cost, but also other characteristics of the product. It is based on the use of company resources and functions (actions performed at each stage of the production cycle) that are involved in the manufacturing of goods and the provision of services.
This is an alternative to traditional approaches. FSA differs from them in the following qualities:
- Information is presented in a form that is understandable to staff. Employees involved in the business process have access to data that is presented in an understandable way.
- Overhead costs are allocated according to the principle of accurate calculation of the use of company resources. At the same time, information on the processes during which certain goods or services were provided was disclosed in detail. This allows you to evaluate the impact on the cost of certain costs.
Functional-cost analysis is a convenient technique that discloses information about company expenses. With its help, a whole range of work is performed. Moreover, the general principles of the methodology can be applied both in the current and in the strategic management of the organization.
Application of analysis results
Considering the goals and objectives of the functional-cost analysis, it should be noted that with its help many types of work are performed:
- Real information is collected and submitted in an accessible form on the effectiveness of responsibility centers at the studied object.
- Directions are determined and a general analysis of the cost indicator of various business processes is carried out. For example, research can be conducted on production, marketing, marketing, service, quality monitoring and more.
- A comparative analysis is carried out and the choice of the most cost-effective business process, as well as the technology for its implementation, is substantiated.
- Conducting analytical activities aimed at establishing and substantiating the functions of structural units of the object of study. This allows you to improve the quality of the finished products of the organization.
- The main, additional, as well as unnecessary costs in the course of the implementation of core activities are identified and investigated.
- Developed and compared ways to reduce the cost of manufacturing products, sales and management. This is made possible by streamlining the functions of workshops, production sites and other structural units.
- An analysis of the proposed improvements integrated into the company’s activities is carried out.
Goals and objectives of the method
The methodology involves the development and practical application of special models. Considering the goals and objectives of the functional-cost analysis, it can be noted that it is needed to improve the organization. Moreover, when using the technique, efficiency is improved in different directions. So, indicators of labor input, cost, productivity are improving. When building models, it is possible to obtain a large amount of information important for decision-making. Moreover, the results of such studies can be very unexpected for managers.
The purpose of the functional-cost analysis is to obtain the required information about the effectiveness of the centers of responsibility of the organization. This becomes possible due to the construction of a system of indicators of cost and time expenditure, as well as during the analysis of labor costs, labor input, and a number of other relative indicators.
During operational management, the technique allows you to formulate recommendations on actions that will increase profits, as well as increase the efficiency of the company. When conducting strategic management, important information can be obtained for making decisions on reorganization, assortment change, new production, diversification, etc.
The task of functional-cost analysis is to provide data on how to correctly redistribute company resources in order to get maximum benefit. For this, the possibilities of factors that have the greatest influence on the final result are determined. This, for example, can be quality, cost reduction, maintenance, optimization of labor intensity, etc. Based on the research, decisions are made on financing the most appropriate areas.
ICA models are used to reduce production costs, increase productivity, reduce time costs and improve the technology of manufacturing finished products.
Methodology algorithm
There are several main stages of the functional-cost analysis. This allows you to get a reliable result of the study.
At the first stage, it is determined which functions are performed sequentially during the production of finished products. Having compiled a list of processes that raw materials undergo in the process of their transformation into a final product, they are divided into two groups. The first category includes functions that affect the value of the product, and the second - not affecting. After that, the process is optimized. It is necessary to reduce or remove completely (if possible) all steps that do not affect the value of the goods. This way you can reduce costs.
At the second stage of the functional-cost analysis, for each individual process, the costs for the entire reporting period are determined. It also counts the number of working hours spent performing a similar function.
The third stage involves the calculation of the amount of costs that the company incurs in the production process and the implementation of each process. So, for example, the work of the machine is characterized by direct and overhead costs, which in total leave 250 thousand rubles. in year. During this time, the equipment will produce 25 thousand units. The approximate cost of the source of costs is 10 rubles. on one product. An hour the machine makes 6 products, so an alternative unit of measurement may be a cost indicator of 60 rubles. in hour. In the process of calculating the amount of costs, you can use both equivalents.
Considering the basics of functional-cost analysis, it can be noted that in the course of such work two types of source of costs can be applied:
- By function (activity drivers). It shows how the cost object affects the level of detail of the process.
- By resources (resource drivers). Reflects how levels of functional activity affect costs.
In the fourth stage, after determining the source of costs, for each stage of the production cycle, a final calculation of the costs that arise in the manufacture of a particular product is carried out.
In each case, the stages of production are considered on a different scale. He is chosen in accordance with the objectives of the study. If the model is too detailed, the calculation of the PSA can be complicated. Even before the start of the study, the degree of complexity of this process is determined. It depends on the costs that the organization allocates for the study.
How to apply the result of the study
Functional-cost analysis is an effective system that allows solving a number of issues. They are related to the level of profitability that the manufacturer planned. With the help of the FSA, one can answer the following questions:
- Does the market set the price level, or can the manufacturer choose for what price it is optimal to sell finished products?
- Is it obligatory to increase expenses, the premium of which was calculated according to the FSA method?
- Should costs be increased proportionally, if there is a justified need for this, or should only certain areas be financed?
- How do FSA indicators compare with the level of the final price of products?
We can say that functional-cost analysis is a technique that allows you to assess the level of profit that an organization can get when manufacturing certain products.
If the costs are correctly estimated, the income before tax will be equal to the difference between the sale price and the costs that were calculated by the FSA method. At the same time, it will be possible to determine at the planning stage what production will be unprofitable. The selling price in this case will be less than the total costs. You can make appropriate changes in a timely manner to prevent negative consequences.
Improving the efficiency of business processes
Functional cost analysis allows to increase production efficiency. This procedure is carried out in three stages:
- Analysis of production processes, which allows to identify opportunities for improving the procedures for their implementation.
- Identify the reasons that explain the occurrence of unproductive costs, and also find ways to eliminate them.
- Monitoring is carried out and appropriate technologies are introduced into the production process.
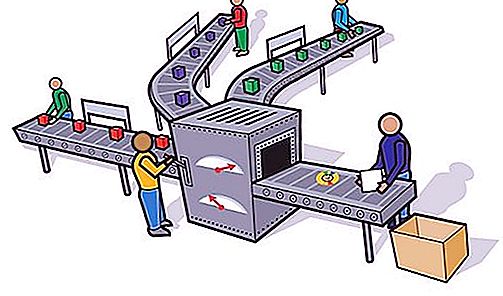
You can rebuild the company to reduce the time, cost, labor spent using the functional-cost analysis. FSA can reduce them by improving production technology. To do this, a number of actions are carried out:
- A list of processes is compiled that are ranked by cost, time spent and labor input.
- Choose the function, the cost of which will be the largest.
- The time required for carrying out certain production processes is reduced.
- Unnecessary production steps are eliminated.
- Organized the joint use of all the required functions.
- Redistribute resources, freeing up capital in the process of improving technology.
Such actions can improve production, improve the quality of the result of the organization. At the same time, different stages of the product manufacturing process are compared, rational technologies are selected. They are allocated funding. Unprofitable, unreasonably costly processes are improved or eliminated completely.
The information obtained during the FSA, apply various analytical methods, for example, strategic, cost, time analysis. A functional cost analysis of personnel can also be carried out, the data of which are used during the study of labor intensity indicators. The issues of determining the target value of the finished product and the price that arises from the product life cycle are also being addressed.
Based on the FSA methodology, an enterprise budget system is being formed. First, the volume and price of work, as well as the amount of resources are determined. If this area is profitable, a budget is created to fulfill the production task. The decisions in this case are focused and informed. Resources are allocated according to the optimal scheme. Based on this, a reasonable budget system is formed.
FSA Benefits
Functional-value analysis technology has both a number of advantages and disadvantages. The positive qualities of the technique include:
- The analyst receives accurate information about which components the value of the finished product is made up of. This allows you to make informed decisions in the strategic planning of the organization in the context of determining prices for finished products, the correct ratio of products. Managers can make the right decision about whether to produce certain products on their own or to purchase them for the purpose of further processing.
- Based on the research, you can determine whether it is necessary to finance research in this industry, to automate production processes, to promote goods or services, etc.
- Clarity in the field of production functions. Due to this, the organization can pay more attention to expensive production processes, their efficiency, as well as reduce the volume of operations that do not add additional value to the product.
The disadvantages of the method
Functional cost analysis of costs has some disadvantages:
- If the details of the process are incorrectly detailed, the calculation may be difficult, since the model becomes overloaded with details. She's getting too complicated.
- Managers often underestimate the importance of collecting data on the sources of cost formation by function.
- To qualitatively implement the methodology, you need special software.
- Due to organizational changes, the model quickly becomes obsolete.
- The implementation process is not always considered seriously enough by management; it may not be taken into account when making decisions.
FSA application example
In order to better understand the features of the functional-cost analysis of the system of production functions, it is necessary to consider its application by example. Almost any company can set prices for products incorrectly, especially if it produces and sells a large number of products. To understand why such errors occur, we can consider the work of two plants.
Manufactures make ordinary pens for writing. So, at the first plant 1 million blue ball-point pens are produced annually, and at the second - 100 thousand pieces. In order to use the production capacities to the maximum, in the second factory, in addition to blue pens, they produce another 65 thousand black, 15 thousand red, 13 thousand purple pens and a whole series of other varieties. In general, for the year the second plant produces up to 1000 types of different pens. The volume of production here ranges from 500 to 1 million units. in year. Thus, it happens that the quantity of production of the first and second plants coincides, reaching one million units of production per year.
It can be assumed that in this case both industries need the same number of jobs, spend the same number of hours, materials, etc. But there are significant differences in the organization of production processes. The second plant employs more staff. The staff includes specialists who deal with issues:
- settings and control of units, machines, lines, etc.;
- equipment checks after configuration;
- receipt and verification of raw materials, materials and parts that are used in the production process;
- movement of materials, finished products, shipment to points of sale;
- marriage processing;
- design, implementation of design changes;
- conclusion of transactions with suppliers;
- planning for the supply of parts and raw materials;
- modernization and programming of a more extensive software system than at the first factory.
The second plant has higher downtime, more overtime hours. Warehouses are reloaded, more improvements and waste. These and many other issues lead to price mismatch with market realities.
To increase profits, the second plant should reduce the production of simple blue pens, of which there are enough on the market, and produce colored varieties. Such goods sell more expensive than blue pens (although their cost of production is almost the same as blue ones). To determine which products, how much to release, how to cut costs, the FSA will help.