Many motorists repair engines of their cars on the floor of the garage or on a workbench. This is always inconvenient, due to the constant lifting of weights, tilting of a bulky cylinder block or cylinder head. All these factors lead to excessive fatigue of a motorist-mechanic and a decrease in the quality of engine assembly. To facilitate their work, the craftsmen have developed many homemade tilter designs for the engine.
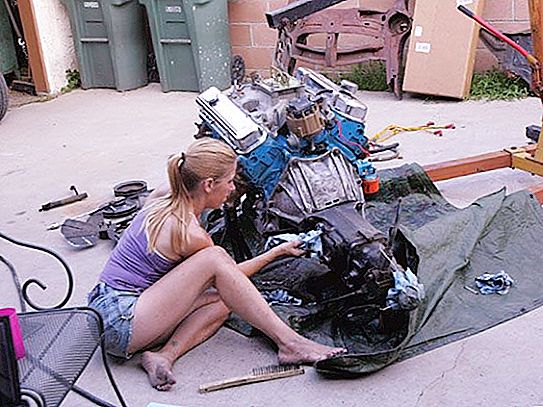
Options for homemade tilter designs
In fact, there are not many options. In the West, complex and bulky home-made constructions are known, like a crane beam, almost with hydraulic drives.
In domestic conditions, motorists assemble the simplest designs from what is at hand. From home-made tilters for the engine, two-support and cantilever versions of the design are known. The simplest to manufacture is the latest design. Its characteristics are sufficient for overhaul of almost any engine of a car weighing from 150 to 250 kg.
Drawings and overall dimensions
Before proceeding with the manufacture of the unit, it is necessary to study in detail the existing samples of stands for engine repair. The sample is selected for the urgent needs of an amateur mechanic. We assess the availability of materials, sizes for the convenience of working in a small garage. The weight of the permissible load is calculated in accordance with the type of engine that is supposed to be repaired.
According to the results of the study of existing structures, a draft drawing of the most optimal version of the cantilever tilter was developed. Overall dimensions on the diagram are given in millimeters.
In the sketch, the designations D 60 and D 52 correspond to a diameter of 60 and 52 mm.
Materials for the manufacture
Due to the fact that the tilter for the engine will have to work in harsh conditions of physical stress associated with the weight of the engine, high demands are placed on the materials.
The following materials are used for manufacturing:
- steel square profile 70 x 70 with a wall thickness of 3 mm, a length of 3 m;
- steel pipe with an outer diameter of 60 mm, an inner diameter of 53 mm, a length of 245 mm;
- steel pipe with an outer diameter of 47 mm, a length of 480 mm;
- steel channel with an internal side width of 70 mm, a wall thickness of 3-4 mm, a length of 280 mm;
- flange for bolting to the engine - 1 pc.
Tools and hardware for assembly of the stand
To connect the metal structures from a steel channel and a square profile, a welding machine is required, which allows working with an electrode with a cross section of at least 3-4 mm. In addition, for cutting you will need a grinding machine with a cutting disc for metal with a diameter of 115-125 mm. To ensure a bolted connection of prefabricated parts, a drill with the ability to work with a drill with a diameter of up to 14-20 mm is required. M12 bolts are also needed to assemble the structure.
You will also need a set of files for cutting burrs and uneven edges, removing flaws in metal cutting. It does not hurt to buy an emery cloth to clean the surface from rust before painting.
Engine tilter assembly
The first step is cutting the channel and square profile in accordance with the sketch. Next, a vertical stand is made of a profile and welded to a square from a channel. Then the structure is reinforced with metal slopes, which can be made from scraps of parts.
After that, from the cut square profile, the base is welded - the tilter stand for engine repair. At the place of bolting to the base of the vertical rack, preparatory work is carried out, steel bushings are inserted and welded to strengthen the structure.
Then proceed with the final assembly of the engine tilter. The stand is connected to the stand by welding and M12 bolts.
A horizontal pipe with an outer diameter of 60 mm and an inner 52 mm is attached to the vertical stand by welding. A horizontal axis is inserted into this part. It can be made of a steel pipe with a diameter of 47 mm with a welded flange for bolting the cylinder block or cylinder head.
In the horizontal axis, you can drill through holes every 45 ° along the radius, for the possibility of fixing the position in space with the pins, after turning the attached motor to the required angle.
The assembled engine tilter should be cleaned and primed, and then painted with nitro enamel to prevent metal corrosion and improve the quality of overhauls.
If a collapsible design is not required, the vertical stand can be attached to the stand not by bolting, but by welding. After that, the device will allow you to work with heavier motors. As you know, 1 cm of the weld can withstand 100 kg of load. And that is a lot. You can imagine what kind of cargo a homemade unit boiled over all edges of joints can withstand. It can even turn out a tilter of the YaMZ engine.
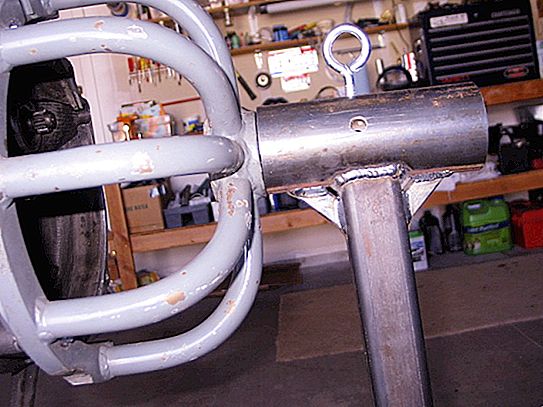